Скачать .docx |
Курсовая работа: Расчет редуктора 3
содержание
1. Выбор электродвигателя, кинематический и силовой расчет привода 4
2. Расчет зубчатых колес редуктора.. 6
3. Предварительный расчет валов редуктора.. 11
4.1. Конструктивные размеры шестерни и колес. 13
4.2. Конструктивные размеры корпуса редуктора. 13
5.ПОДБОР И ПРОВЕРКА ДОЛГОВЕЧНОСТИ ПОДШИПНИКА, ОПОРНЫЕ РЕАКЦИИ.. 16
6.ЗАПАС УСТАЛОСТНОЙ ПРОЧНОСТИ. Уточненный расчет валов.. 22
Задание на проектирование
Спроектировать одноступенчатый горизонтальный цилиндрический косозубый редуктор для привода к ленточному конвейеру.
Кинематическая схема:
1. Электродвигатель.
2. Муфта электродвигателя.
3. Шестерня.
4. Колесо.
5. Муфта барабана.
6. Барабан ленточного конвейера.
Технические требования: мощность на барабане конвейера Рб =8,2 кВт, частота вращения барабана nб =200 об/мин.
1. Выбор электродвигателя, кинематический и силовой расчет привода
КПД пары цилиндрических зубчатых колес ηз = 0,96; коэффициент, учитывающий потери пары подшипников качения, ηп.к = 0,99; КПД муфты ηм = 0,96.
Общий КПД привода
ηобщ =ηм 2 ·ηп.к 3 ·ηз = 0,972 ·0,993 ·0,96=0,876
Мощность на валу барабана Рб =8,2 кВт, nб =200 об/мин. Требуемая мощность электродвигателя:
Рдв
= =
=
9.36 кВт
Интервал рекомендуемых оборотов двигателя:
Nдв
=
nб
·(2...5)== 400…1000 об/мин
Выбираем электродвигатель, исходя из требуемой мощности Рдв =9,36 кВт, электродвигатель трехфазный короткозамкнутый серии 4А, закрытый, обдуваемый, с синхронной частотой вращения 750 об/мин 4А160M6У3, с параметрами Рдв =11,0 кВт и скольжением 2,5% (ГОСТ 19523-81). Номинальная частота вращения двигателя:
nдв
= об/мин.
Передаточное число i= u= nном / nб = 731/200=3,65
Определяем частоты вращения и угловые скорости на всех валах привода:
nдв = nном = 731 об/мин
n1 = nдв = 731 об/мин
об/мин
nб = n2 = 200,30 об/мин
,
где - частота вращения электродвигателя;
- номинальная частота вращения электродвигателя;
- частота вращения быстроходного вала;
- частота вращения тихоходного вала;
i = u - передаточное число редуктора;
- угловая скорость электродвигателя;
-угловая скорость быстроходного вала;
-угловая скорость тихоходного вала;
-угловая скорость приводного барабана.
Определяем мощность и вращающий момент на всех валах привода:
Рдв =Ртреб = 9,36 кВт
Р1 =Рдв ·ηм = 9.36·0,97=9,07 кВт
Р2 =Р1 ·ηп.к 2 ·ηз = 9,07·0,992 ·0,96=8,53 кВт
Рб =Р2 · ηм ·ηп.к = 8.53·0,99·0,97=8,19 кВт
где - мощность электродвигателя;
- мощность на валу шестерни;
- мощность на валу колеса;
- мощность на валу барабана.
Определяем вращающий момент электродвигателя и вращающие моменты на всех валах привода:
где - вращающий момент электродвигателя;
- вращающий момент быстроходного вала;
- вращающий момент тихоходного вала;
- вращающий момент приводного барабана.
2. Расчет зубчатых колес редуктора
Для шестерни и колеса выбираем материалы со средними механическими характеристиками:
- для шестерни сталь 45, термическая обработка – улучшение, твердость НВ 230;
- для колеса – сталь 45, термическая обработка – улучшение, твердость НВ 200.
Рассчитываем допускаемые контактные напряжения по формуле:
,
где σ H lim b – предел контактной выносливости при базовом числе циклов;
К HL – коэффициент долговечности;
[SH ] – коэффициент безопасности.
Для углеродистых сталей с твердостью поверхностей зубьев менее НВ 350 и термической обработкой (улучшением)
σ H lim b = 2НВ+70;
К HL принимаем равным 1, т.к. проектируемый срок службы более 5 лет; коэффициент безопасности [SH ] =1,1.
Для косозубых колес расчетное допускаемое контактное напряжение определяется по формуле:
для шестерни =
МПа
для колеса =
МПа.
Тогда расчетное допускаемое контактное напряжение
МПа.
Условие выполнено.
Межосевое расстояние из условий контактной выносливости активных поверхностей зубьев найдем по формуле:
,
где - твердость поверхностей зубьев. Для симметричного расположения колес относительно опор и при твердости материала ≤350НВ принимаем
в интервале (1 – 1,15). Примем
=1,15;
ψba =0,25÷0,63 – коэффициент ширины венца. Принимаем ψba = 0,4;
Ka = 43 – для косозубых и шевронных передач;
u - передаточное число. и = 3,65;
.
Принимаем межосевое расстояние , т.е. округляем до ближайшего целого числа.
Нормальный модуль зацепления принимаем по следующей рекомендации:
mn
= =
мм;
принимаем по ГОСТ 9563-60 mn =2 мм.
Примем предварительно угол наклона зубьев β = 10о и рассчитаем число зубьев шестерни и колеса:
Z1=
Принимаем z1 = 34, тогда число зубьев колеса z2 = z1 · u= 34·3.65=124,1. Принимаем z2 = 124.
Уточняем значение угла наклона зубьев:
Основные размеры шестерни и колеса:
диаметры делительные:
Проверка: мм;
диаметры вершин зубьев:
da 1 = d 1 +2 mn =68,86+2·2=72,86 мм;
da 2 = d 2 +2 mn =251,14+2·2=255,14 мм;
диаметры впадин зубьев:df 1 = d1 - 2 mn =68,86-2·2=64,86 мм;
df
2
=
d2 -
2
=
251,14-2·2=247,14 мм;
определяем ширину колеса : b2=
определяем ширину шестерни: b1 = b2 +5мм =64+5=69 мм.
Определяем коэффициент ширины шестерни по диаметру:
Окружная скорость колес и степень точности передачи:
При такой скорости для косозубых колёс принимаем 8-ю степень точности, где коэффициент нагрузки равен:
КНβ
принимаем равным 1,04.
, т.к. твердость материала меньше 350НВ.
Таким образом, KH = 1,04·1,09·1,0=1,134.
Проверяем контактные напряжения по формуле:
Рассчитываем перегруз:
Перегруз в пределах нормы.
Силы, действующие в зацеплении:
окружная:
;
радиальная:
,
где =200
-угол зацепления в нормальном сечении;
=9,070
-угол наклона зубьев.
осевая:
Проверяем зубья на выносливость по напряжениям изгиба по формуле:
.
,
где =1,1 – коэффициент, учитывающий неравномерность распределения нагрузки по длине зуба (коэффициент концентрации нагрузок);
=1,1 – коэффициент, учитывающий динамическое действие нагрузки (коэффициент динамичности);
-коэффициент, учитывающий форму зуба и зависящий от эквивалентного числа зубьев
Тогда:
Допускаемое напряжение по формуле
.
Для стали 45 улучшенной при твердости НВ≤350 σ0 F lim b =1,8 НВ.
Для шестерни σ0 F limb =1,8·230=415 МПа; для колеса σ0 F limb =1,8·200=360 МПа.
[SF ]=[SF ]΄[SF ]˝ - коэффициент безопасности, где [SF ]΄=1,75, [SF ]˝=1 (для поковок и штамповок). Следовательно, .[SF ]=1,75.
Допускаемые напряжения:
для шестерни МПа;
для колеса МПа.
Находим отношение :
для шестерни ;
для колеса .
Дальнейший расчет следует вести для зубьев колеса, для которого найденное отношение меньше.
Определяем коэффициенты Yβ и KFα :
,
где К Fα - коэффициент, учитывающий неравномерность распределения нагрузки между зубьями;
=1,5 -
коэффициент торцового перекрытия;
n=8 -степень точности зубчатых колес.
Проверяем прочность зуба колеса по формуле:
;
Условие прочности выполнено.
3. Предварительный расчет валов редуктора
Диаметры валов определяем по формуле:
.
Для ведущего вала [τк ] = 25 МПа; для ведомого [τк ] = 20 МПа.
Ведущий вал:
Для двигателя марки 4А 160М6У3 =48 мм. Диаметр вала dв1
=48
Примем диаметр вала под подшипниками d п1 =40 мм
Диаметр муфты d
м
=0,8·=
=38,4 мм. Принимаем d
м
=35 мм.
Свободный конец вала можно определить по приближенной формуле:
,
где dп – диаметр вала под подшипник.
Под подшипниками принимаем:
Тогда l
=
Схематичная конструкция ведущего вала изображена на рис. 3.1.
|

|

|

|

|
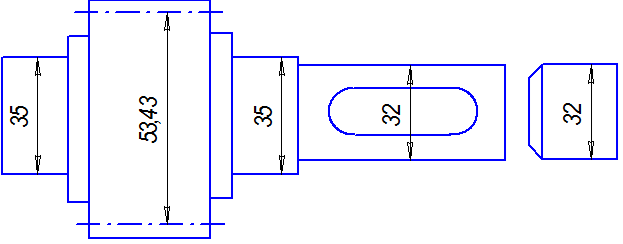
Рис. 3.1. Конструкция ведущего вала
Ведомый вал.
Диаметр выходного конца вала:
, принимаем ближайшее значение из стандартного ряда
Под подшипниками берем
Под зубчатым колесом
Схематичная конструкция ведомого (тихоходного) вала показана на рис.3.2.
|
|
|
|

Рис. 3.2. Конструкция ведомого вала
Диаметры остальных участков валов назначают исходя из конструктивных соображений при компоновке редуктора.
4. КОМПОНОВКА РЕДУКТОРА
4.1. Конструктивные размеры шестерни и колес
Шестерню выполняем за одно целое с валом. Её размеры:
ширина
диаметр
диаметр вершины зубьев
диаметр впадин .
Колесо кованое:
ширина
диаметр
диаметр вершины зубьев
диаметр впадин
диаметр ступицы
длина ступицы ,
принимаем
Толщина обода:
принимаем
Толщина диска:
4.2. Конструктивные размеры корпуса редуктора
Толщина стенок корпуса и крышки:
, принимаем
, принимаем
.
Толщина фланцев поясов корпуса и крышки:
верхнего пояса корпуса и пояса крышки:
нижнего пояса корпуса:
, принимаем
.
Диаметр болтов:
фундаментальных ; принимаем болты с резьбой М16;
крепящих крышку к корпусу у подшипников
; принимаем болты с резьбой М12;
соединяющих крышку с корпусом ; принимаем болты с резьбой М8.
Первый этап служит для приближенного определения положения зубчатых колес относительно опор для последующего определения опорных реакций и подбора подшипников.
Компоновочный чертеж выполняется в одной проекции - разрез по осям валов при снятой крышке редуктора; масштаб 1:1.
Размеры корпуса редуктора:
принимаем зазор между торцом шестерни и внутренней стенкой корпуса (при наличии ступицы зазор берем от торца ступицы) ; принимаем А1
=10мм;
при наличии ступицы зазор берется от торца ступицы;
принимаем зазор от окружности вершин зубьев колеса до внутренней стенки корпуса ;
принимаем расстояние между наружным кольцом подшипника ведущего вала и внутренней стенкой корпуса ; если диаметр окружности вершин зубьев шестерни окажется больше наружного диаметра подшипника, то расстояние
надо брать от шестерни.
Предварительно намечаем радиальные шарикоподшипники однорядные средней серии; габариты подшипников выбираем по диаметру вала в месте посадки подшипников и
.(Таблица 1).
Таблица 1:
Габариты намеченных подшипников
Вал |
Условное обозначение подшипника |
d |
D |
B |
Грузоподъемность, кН |
|
размеры, мм |
С |
С0 |
||||
Быстроходный |
208 |
40 |
80 |
18 |
32,0 |
17,8 |
Тихоходный |
211 |
55 |
100 |
21 |
43,6 |
25,0 |
Решаем вопрос о смазывании подшипников. Принимаем для подшипников пластичный смазочный материал. Для предотвращения вытекания смазки внутрь корпуса и вымывания пластичного смазочного материала жидким маслом из зоны зацепления устанавливаем мазеудерживающие кольца.
Эскизная компоновка изображена на рис. 4.1.
5.ПОДБОР И ПРОВЕРКА ДОЛГОВЕЧНОСТИ ПОДШИПНИКА, ОПОРНЫЕ РЕАКЦИИ
Из предыдущих расчетов имеем:
Определяем опорные реакции.
Расчетная схема вала и эпюры изгибающих моментов изображены на рис. 5.1
В плоскости YOZ:
Проверка:
в плоскости XOZ:
Проверка:
Суммарные реакции в опорах А и В:
Определяем моменты по участкам:
в плоскости YOZ:
сечение 1:
;
сечение 2: M=0
M
Сечение 3: М
M
в плоскости XOZ:
сечение 1: ;
=
сечение2:
сечение3:
Строим эпюры изгибающих моментов.
Подбираем подшипник по наиболее нагруженной опоре. Намечаем радиальные шариковые подшипники 208: d =40 мм; D =80 мм; В =18 мм; С =32,0 кН; Со = 17,8кН.
Эквивалентная нагрузка определяется по формуле:
,
где RB =2267,3 Н
=1 (вращается внутреннее кольцо);
- коэффициент безопасности для приводов ленточных конвейеров;
- температурный коэффициент.
Отношение ; этой величине соответствует
.
Отношение ; Х=0,56 и
Y
=2,15
Расчетная долговечность по формуле:
где - частота вращения ведущего вала.
Ведомый вал несет такие же нагрузки, как и ведущий:
Расчетная схема вала и эпюры изгибающих моментов изображены на рис. 5.2
Определяем опорные реакции.
В плоскости YOZ:
Проверка:
В плоскости ХOZ:
Проверка:
Суммарные реакции в опорах А и В:
Определяем моменты по участкам:
в плоскости YOZ:
сечение 1: при х=0, ;
при x
=
l
1
, ;
сечение 2: при x
=
l
1
, ;
при х= l 1 + l 2 ,
сечение 3:;
в плоскости XOZ:
сечение 1: при х=0, ;
при x
=
l
1
, ;
сечение 2: при х= l 1 + l 2 ,
сечение 3: при x = l 1 + l 2 + l 3 ,
.
Строим эпюры изгибающих моментов.
Подбираем подшипник по наиболее нагруженной опоре и определяем их долговечность. Намечаем радиальные шариковые подшипники 211: d =55 мм; D =100 мм; В =21 мм; С =43,6 кН; Со = 25,0 кН.
Эквивалентная нагрузка определяется по формуле:
,
где RA =4290,4 Н
=1 (вращается внутреннее кольцо);
- коэффициент безопасности для приводов ленточных конвейеров;
- температурный коэффициент.
Отношение ; этой величине соответствует e=0,20.
Отношение , тогда Х=1, Y=0. Поэтому
Расчетная долговечность, млн. об.
Расчетная долговечность, ч.
где - частота вращения ведомого вала.
6.ЗАПАС УСТАЛОСТНОЙ ПРОЧНОСТИ. Уточненный расчет валов
Примем, что нормальные напряжения изгиба меняются по симметричному циклу, а касательные от кручения – по пульсирующему.
Уточненный расчет валов состоит в определении коэффициентов запаса прочности s для опасных сечений вала и сравнении их с требуемыми значениями [s]. Прочность соблюдена при .
Определяем суммарные изгибающие моменты. Значения изгибающих моментов по участкам берем с эпюр.
Сечение 1: при х=0, ;
при х=
l
3
, ;
Сечение 2: при х=
l
3
, ;
при х=
l
3
+
l
2
, ;
Сечение 3: при х=
l
3
+
l
2
, ;
при х=
l
3
+
l
2
+
l
1
, .
Крутящий момент:
.
Определяем опасные сечения. Для этого схематически изображаем вал (рис. 8.1)
Рис. 8.1 Схематическое изображение ведущего вала
Опасными являются два сечения: под левым подшипником и под шестерней. Они опасны, т.к. сложное напряженное состояние (изгиб с кручением), изгибающий момент значительный.
Концентраторы напряжений:
1) подшипник посажен по переходной посадке (напрессовка менее 20 МПа);
2) галтель (или проточка).
Определяем коэффициент запаса усталостной прочности.
При диаметре заготовки до 90мм среднее значение предела прочности для стали 45 с термообработкой - улучшение
.
Предел выносливости при симметричном цикле изгиба:
Предел выносливости при симметричном цикле касательных напряжений:
.
Сечение А-А. Концентрация напряжений обусловлена посадкой подшипника с гарантированным натягом:
Т.к. давление напрессовки меньше 20 МПа, то снижаем значение данного отношения на 10 %.
для упомянутых выше сталей принимаем и
Изгибающий момент из эпюр:
Осевой момент сопротивления:
Амплитуда нормальных напряжений:
Среднее напряжение:
Полярный момент сопротивления:
Амплитуда и среднее напряжение цикла касательных напряжений по формуле:
Коэффициент запаса прочности по нормальным напряжениям по формуле:
Коэффициент запаса прочности по касательным напряжениям по формуле:
Результирующий коэффициент запаса прочности для сечения по формуле:
Результирующий коэффициент больше допустимых норм (1,5÷5). Следовательно, диаметр вала нужно уменьшить, что в данном случае делать не следует, т.к. такой большой коэффициент запаса прочности объясняется тем, что диаметр вала был увеличен при конструировании для соединения его стандартной муфтой с валом электродвигателя.
Определяем суммарные изгибающие моменты. Значения изгибающих моментов по участкам берем с эпюр.
Сечение 1: при х=0, ;
при х=
l
1
, ;
Сечение 2: при х=
l
1
, ;
при х=
l
1
+
l
2
, ;
Сечение 3: при х=
l
1
+
l
2
, ;
при х=
l
1
+
l
2
+
l
3
,
Крутящий момент:
.
Определяем опасные сечения. Для этого схематически изображаем вал
(рис. 8.2)
Рис. 8.2 Схематическое изображение ведомого вала
Опасными являются два сечения: под правым подшипником и под шестерней.
Определяем коэффициент запаса усталостной прочности.
При диаметре заготовки до 90мм среднее значение предела прочности для стали 45 с термообработкой - нормализация
.
Предел выносливости при симметричном цикле изгиба:
Предел выносливости при симметричном цикле касательных напряжений:
Сечение А-А. Считаем на усталость сечение под колесом, оно опасное, т.к. сложное напряженное состояние, значительный изгибающий момент, концентрация напряжения от двух концентраторов: шпоночное отверстие и посадка с гарантированным натягом.
d=
52 мм
; и
; масштабные факторы:
и
.
Для вала диаметром выбираем призматическую шпонку с сечением: b
=
18 мм,
h
=
11 мм
и глубиной паза вала
.
Для упомянутых выше сталей принимают коэффициенты и
.
Изгибающий момент:.
Момент сопротивления кручению:
W
к нетто
Момент сопротивления изгибу:
Амплитуда нормальных напряжений:
Среднее напряжение:
Амплитуда и среднее напряжение цикла касательных напряжений:
Коэффициент запаса прочности по нормальным напряжениям:
Коэффициент запаса прочности по касательным напряжениям:
Результирующий коэффициент запаса прочности для сечения:
Сечение Б-Б. Концентрация напряжений обусловлена посадкой подшипника с гарантированным натягом:
;
принимаем и
Изгибающий момент из эпюр:
Осевой момент сопротивления:
Полярный момент сопротивления:
Амплитуда нормальных напряжений:
Среднее напряжение:
Амплитуда и среднее напряжение цикла касательных напряжений:
Коэффициент запаса прочности по нормальным напряжениям:
Коэффициент запаса прочности по касательным напряжениям:
Результирующий коэффициент запаса прочности для сечения по формуле:
Т.к. результирующий коэффициент запаса прочности под подшипником меньше 3,5, то уменьшать диаметр вала не надо.
.
7. Расчет шпонок
Материал шпонок – сталь 45 нормализованная.
Напряжения смятия и условие прочности определяем по формуле:
.
Максимальные напряжения смятия при стальной ступице [σсм
] = 100120 МПа, при чугунной [σсм
] = 50
70 МПа.
Ведущий вал: d
=35 мм
, , t1
=5 мм,
l
=56 мм
, Мк1
=
.
Ведомый вал: d
=50 мм
, , t1
=5,5 мм,
l
=70 мм
, Мк2
=
.
8.ВЫБОР СМАЗКИ
Смазывание зубчатого зацепления производится окунанием зубчатого колеса в масло, заливаемое внутрь корпуса до уровня, обеспечивающего погружение колеса примерно на 10 мм. Объём масляной ванны определяем из расчёта 0,25 дм масла на 1 кВт передаваемой мощности:
Устанавливаем вязкость масла. При контактных напряжениях =400,91 МПа и скорости
рекомендуемая вязкость масла должна быть примерно равна
Принимаем масло индустриальное И-30А (по ГОСТ20799-75).
9.СБОРКА РЕДУКТОРА
Перед сборкой внутреннюю полость корпуса редуктора тщательно очищают и покрывают маслостойкой краской.
Сборку производят в соответствии со сборочным чертежом редуктора, начиная с узлов валов:
на ведущий вал мазеудерживающие кольца и шарикоподшипники, предварительно нагретые в масле до 80-1000 С;
в ведомый вал закладывают шпонку и напрессовывают зубчатое колесо до упора в бурт вала; затем надевают распорную втулку, мазеудерживающие кольца и устанавливают шарикоподшипники, предварительно нагретые в масле.
Собрание валы укладывают в основание корпуса редуктора и надевают крышку корпуса, покрывая предварительно поверхность стыка крышки и корпуса спиртовым лаком. Для центровки устанавливают крышку на корпус с помощью двух конических штифтов; затягивают болты, крепящие крышку к корпусу.
После этого в подшипниковые камеры ведомого вала закладывают пластичную смазку, ставят крышки подшипников с комплектом металлических прокладок для регулировки.
Перед постановкой сквозных крышек в проточки закладывают резиновые армированные манжеты. Проверяют проворачиванием валов отсутствие заклинивания подшипников и закрепляют крышки болтами.
Затем ввертывают пробку маслоспускного отверстия с прокладкой и жезловый указатель.
Заливают в корпус масло и закрывают смотровое отверстие крышкой с прокладкой из технического картона; закрепляют крышку болтами.
Собранный редуктор обкатывают и подвергают испытанию на стенде по программе, устанавливаемой техническими условиями.
ЛИТЕРАТУРА
1. Курсовое проектирование деталей машин: Учебное пособие. /С.А. Чернавский, К.Н. Боков, И.М. Чернин и др. – 2-е изд., переработанное и дополненное. –М.: Машиностроение, 1988.-416 с.:ил.
2. Шейнблит А.Е. Курсовое проектирование деталей машин: Учебное пособие. –М.: Высшая школа. 1991.-43 с.: ил.